Common EMF liner type & processing technology
In the selection process of the electromagnetic flowmeter, as a qualified industrial control technician, you need to understand the important parameters that must be involved in the selection of the electromagnetic flowmeter in order to make a correct selection of the required flowmeter .
These parameters mainly include the following points: 1. Pressure 2. Temperature 3. Measuring medium 4. Pipe material 5. Pipe diameter, judging whether the medium is high temperature and corrosive, and knowing the conductivity of the medium. This article focuses on how to choose the inner lining of the electromagnetic flowmeter and briefly introduces the processing technology of the inner lining.
Why do electromagnetic flowmeters need to be lined? This starts with the measurement principle of electromagnetic flowmeters. Electromagnetic flowmeters generally have a set of coils and two electrodes. Of course, some models now use three electrodes in order to enhance the measurement effect. The function of the coil of the electromagnetic flowmeter is to add an electric field to the fluid. The flowing conductive liquid is equivalent to a conductor. According to Faraday's law of electromagnetic induction, when the conductor cuts the magnetic field line, an electromotive force proportional to the speed will be generated correspondingly. The function of the electrode is to measure This induced electromotive force, so only the electrode in the measuring tube is connected with the conductive liquid, and the other part is the inner lining, so the electromagnetic flowmeter can work normally if insulation is ensured. If the section of the metal pipe with the magnetic field is also in contact with the liquid, there will be a short circuit between the conductive liquid measured by the electromagnetic flowmeter and the metal pipe, there will be conduction, and the electric potential will be conducted away so that the electromagnetic flowmeter cannot measure the electric potential. Therefore, the inside of the electromagnetic flowmeter is lined.
When measuring the flow rate, the conductive liquid flows through a magnetic field perpendicular to the direction of flow at a speed V. The flow of the conductive liquid induces a voltage proportional to the average flow rate, and the induced voltage signal passes through two or more than the liquid directly The touched electrodes are picked up and sent to the converter through the cable for intelligent processing, and then LCD display or conversion into standard signals 4-20ma and 0-1khz output. In this way, the electromagnetic flowmeter can measure the flow rate of the conductive fluid.
Electromagnetic flowmeters can only measure the flow of conductive liquids, so there must be a lining inside. Electromagnetic flowmeter lining materials: In the production and manufacture of electromagnetic flowmeters, in order to meet the roughness requirements of the measuring tube for future measurements, it is often necessary to select excellent lining materials according to the type of fluid. For different lining materials, it is necessary to adopt excellent processing methods. Currently commonly used lining materials are: neoprene, EPDM rubber, polyurethane, fluoroplastic PTFE and PFA. For different pipeline linings, the processing techniques are different. The key points of the different lining techniques briefly described here are for the reference of the flowmeter manufacturer. According to the measurement specifications, the medium used to measure the lining is roughly as follows:
I. Neoprene:
The wear resistance of chloroprene rubber is very strong, so it has good adaptability to fluids with particles. It is suitable for large-diameter sensors above DN300, and is mostly used for measuring water, sewage, weak acid, and weak alkali medium fluids. Generally, it is directly adhered to the inner wall of the stainless steel pipe with a film, and is made by vulcanization. In this process, the surface roughness of the rubber lining is generally relatively high, and special attention should be paid to the flatness of the lap joint during operation, but the relative roughness should be low. For small-caliber neoprene and EPDM rubber linings, it is best to use a mold to pressurize, attach to the inner wall of the catheter and then vulcanize. Decreasing the surface roughness of the lining depends on the surface roughness of the mold core rod and the press and vulcanization process.
II. Polychloride:
Polyurethane rubber, also called Polyurethane.
It has excellent wear resistance, but it is insufficient for corrosiveness, and the temperature should not exceed 80°C. It is generally used in industrial and mining environments with high wear resistance, such as the measurement of media such as slurry and coal slurry.
At present, most domestic polyurethane linings use soft materials, and the pouring process is adopted. The lining roughness not only depends on the surface roughness of the mandrel mold, but also is affected by pouring, exhaust, heating, cooling, and material composition and proportion. . Rigid polyurethane mostly uses polyurethane rubber. The important process point of its forming is to remove the bubbles involved in the injection process, so that the chemical reaction (hardening, crosslinking) can be carried out stably; the process method of centrifugal casting: guarantee The raw materials are in a dry state during storage, and the raw materials are uniformly and smoothly mixed and stirred. To remove air bubbles involved in the raw materials, the rotation speed of the tube is set appropriately, and the temperature of raw material processing, hardening, and crosslinking is well controlled. Lining materials requiring low roughness should use fluoroplastics. The PTFE fluoroplastic lining used for piping, tanks, etc. is usually a metal tube lined with a thin-walled PTFE tube, or a PTFE tube is inserted and then bonded. The main disadvantage of this kind of lining is that it is not resistant to negative pressure, is greatly affected by temperature, and the bonding is often unreliable.
III. Fluoroplastics:
For electromagnetic flowmeters, the excellent fluoroplastic lining is PFA. The main method used for PFA is to inject molten resin and then injection (injection injection molding). The injection molding method is adopted, which is a seamless integral molding. The quality of PFA lining has good chemical resistance, heat resistance, and adhesion resistance (surface finish). Especially in terms of chemical resistance and heat resistance, the use of unique manufacturing technology can reduce internal stress and internal bubbles to avoid cracks, so that the flowmeter is still highly reliable when used in harsh environments sex. For this reason, in the PFA lining manufacturing process, the important management points are the injection temperature (resin viscosity, metal mold temperature), mold cooling control (cooling time, temperature), and resin pressure control. The injection temperature should be set as low as possible to reduce the thermal degradation of PFA resin. In injection molding, the temperature of the metal mold must be evenly maintained above the melting point of the resin. Due to the need for high-precision cooling control, multiple cooling circuits should be set in the metal mold and independent cooling control operations should be performed. While performing cooling control, the resin pressure should also be controlled.
IV. Polytetrafluoroethylene, also called PTFE, also called F4.
One of the more commonly used lining materials, because of its stable chemical properties, it is generally used for sanitary liquids or strong corrosive liquids, such as concentrated acids and alkalis.
V. Polyperfluoroethylene propylene, also called F46.
This material is similar to PTFE, but its wear resistance is stronger than that of PTFE, and the medium temperature can be as high as 100℃.
VI.Ceramic
Ceramic is undoubtedly the best high-end product among all electromagnetic flowmeter lining materials. The disadvantage is that the price is not grounded, the production process is complicated, the process requirements are extremely high, and the price is extremely high.
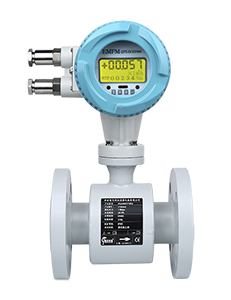